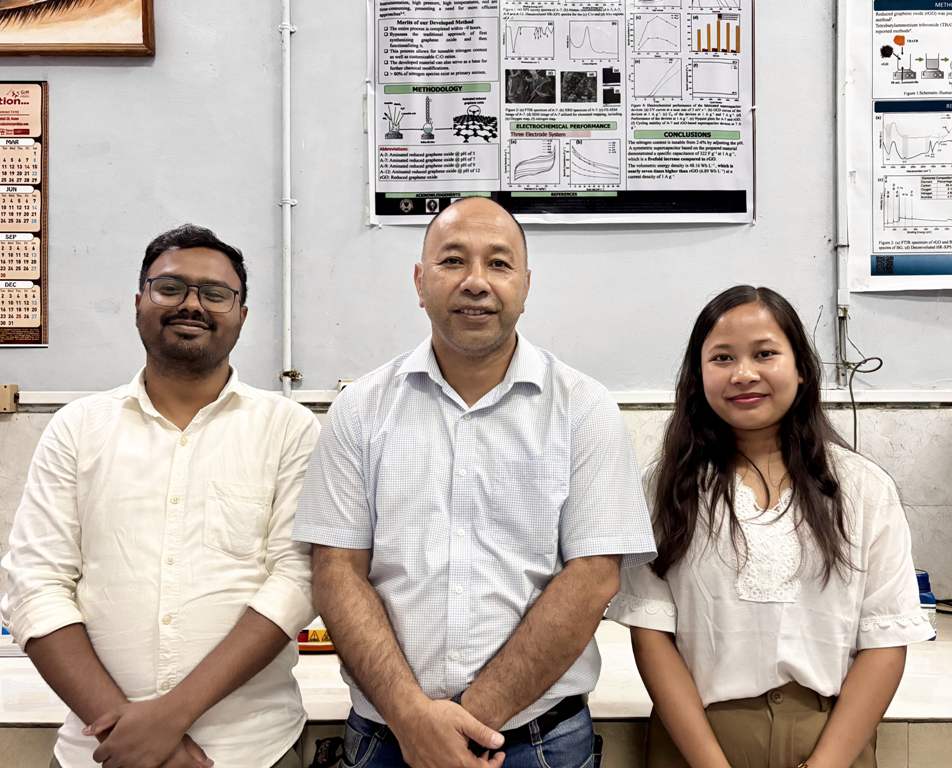
(L-R) Suraj Kumar, Prof. Dipak Sinha, and Priyakshi Bora.
- DIMAPUR — A multi-institute research team led by
Nagaland University (NU) has claimed to have developed a cost-effective method
to create an advanced material for building next-generation energy storage
devices called ‘supercapacitors’.
- “They are gaining attention due to their ability to store
large amounts of energy and charge very quickly, unlike traditional batteries,”
a statement from the university said.
- Stating that these devices are being seen as a potential solution
to the growing demand for more efficient and sustainable energy systems, it
added that a critical part of a supercapacitor’s performance is the material
used for its electrodes, and the high cost of such materials has been a barrier
to widespread use.
- “This research aligns closely with India’s growing focus on
clean energy and environmentally responsible technologies. In this context, the
team developed a new approach to produce aminated graphene, a derivative of
reduced graphene oxide.
Also read: Advisor Mannen lays fountain stone for Khutak Valley Organic Processing Plant
- “This method is notably cost-effective and faster,
completing the entire procedure much more quickly than the traditional
processes. Further, the obtained material also demonstrated good
electrochemical properties. This kind of material can help improve the performance
and lower the cost of energy storage systems. Initial lab tests have shown
promising results. The research has already received an Indian patent. The
research is now at a point where it can be taken further for possible
commercial use,” it said.
- This research was taken up by a team comprising researchers
from NU, Visvesvaraya Technological University (Karnataka), and Nagarjuna
College of Engineering and Technology (Karnataka).
- They have developed a cost-effective method to produce
high-performance ‘functionalised graphene’ supercapacitor material. It features
a wide electrochemical window, good stability, and an impressive energy
density.
- The study was conducted by Suraj Kumar, a DST-INSPIRE fellow
at NU, working under the joint supervision of Prof. Dipak Sinha, Chemistry
department, NU, and Prof. Dinesh Rangappa from Visvesvaraya Technological
University.
- The team also included Priyakshi Bora from NU, Kunal Roy
from Visvesvaraya Technological University, and Dr. Navya Rani M from Nagarjuna
College of Engineering and Technology.
- The findings were published in iScience
(doi.org/10.1016/j.isci.2025.112271), an open-access journal from Cell Press
that provides a platform for original research in the life, physical, social,
earth, social, and health sciences.
- Elaborating on this research, it was stated by Prof. Sinha
that, unlike traditional methods, which are time-consuming and
resource-intensive, the new approach operates under moderate temperature and
pressure conditions, making it energy-efficient, faster, and more suitable for
large-scale production.
- He further explained that the resulting material not only
simplifies the manufacturing process but also delivers significantly enhanced
performance. This enables a supercapacitor with a wide 2.2 V electrochemical
window, an energy density exceeding 50 Wh/kg, and 98% energy retention after
10,000 cycles.
- Notably, it achieves a fivefold increase in gravimetric
energy density compared to its non-aminated counterpart, demonstrating both
scientific novelty and commercial potential.
- Elaborating further on the advantages of this new method,
Suraj explained that traditional methods demand high temperatures, elevated
pressures, and lengthy processing times, which add to the complexity and cost
of production.
- According to him, conventional methods typically involve
converting bulk graphite into graphene oxide, followed by a series of steps to
reduce and functionalise it. In contrast, the developed process is a one-pot
synthesis that directly transforms bulk graphite into aminated graphene.
- He maintained that this process not only reduces time and
resource usage but also operates under moderate temperature and pressure,
making it scalable and energy-efficient. Notably, it stands out as one of the
quickest methods available for producing this material.